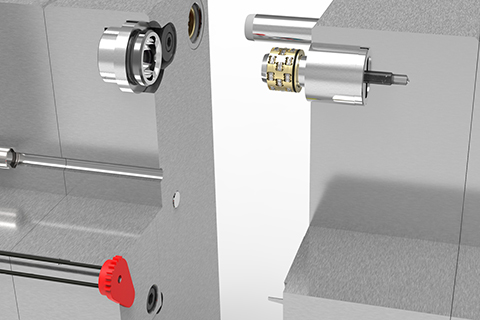
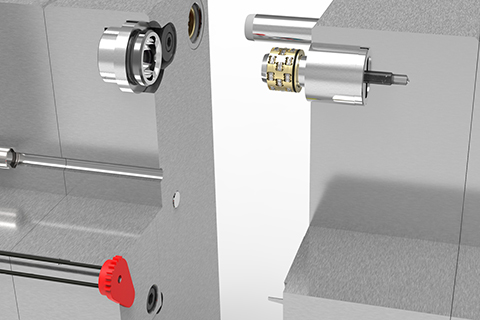
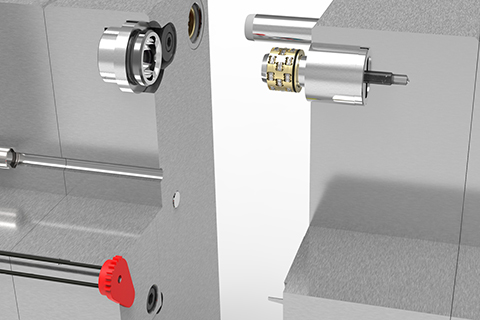
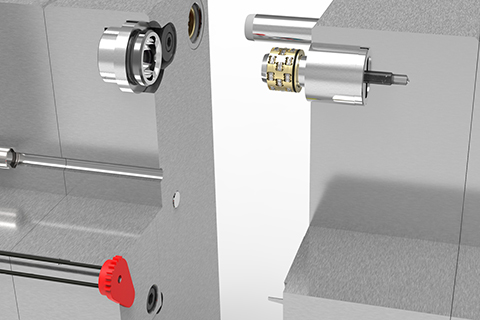
Prodcast und Artikel über Feinzentrierung Plus dynamisch
Flachzentrierungen waren lange das Mass aller Dinge. Sie haben aber einige Nachteile, dazu gehört auch der Abrieb. Agathon bietet mit der Feinzentrierung eine höherwertige Alternative. In diesem Teil geht es um diese Feinzentrierung in der Ausführung Plus dynamisch.
Vor rund zwölf Jahren – also im 2010 – hatte Agathon die ersten Feinzentrierungen entwickelt. Das Ziel war, den Kunden eine höherwertige Alternative zur weitverbreiteten Flachzentrierung anbieten zu können. Und da Agathon spezialisiert ist auf die runde Fertigung, ist die Feinzentrierung Plus gewissermassen auch rund geworden. Doch nicht einfach nur deshalb. Denn «rund» bietet auch sehr viele Vorteile. Eine Bohrung ist in der Regel bereits viel präziser hergestellt aufgrund der Herstellverfahren und dadurch auch kostengünstiger als eine Aufnahmetasche für eine Flachzentrierung.
Funktionsprinzip Feinzentrierung versus Flachzentrierung
Aber noch kurz zu den Funktionsprinzipen beider Varianten. Die Flachzentrierung ist gleitend. Damit sie gleiten kann, hat sie bereits im Neuzustand ein Spiel. Je nach Abmessung ist dieses Spiel bereits bis ein Hundertstel gross. Durch den Abrieb wird dieses Spiel im Laufe der Zeit immer grösser, da ja die Oberflächen aufeinander gleiten und es zu Festkörperreibung kommt. Die Agathon Feinzentrierung dagegen ist spielfrei oder anders gesagt: Die Wälzkörper sind vorgespannt. Es werden Rollen-Wälzkörper eingesetzt mit Linienwälzkontakt, der Linienkontakt schmiegt sich an die Säule und Buchse an. Das alles ergibt eine sehr hohe Tragkraft, sodass selbst schwere Werkzeuge zueinander auszentriert werden können.
Portfolio der Feinzentrierungen wächst
Mittlerweile ist das Produktprogramm gewachsen. Die kleinste Feinzentrierung Plus hat einen Aufnahmedurchmesser von 20 Millimeter und kürzlich hat Agathon das Portfolio nach oben erweitert, damit man bei Werkzeugen eingesetzt werden kann, die rund 800 × 1000 Millimeter Abmessung haben.
Zudem gibt es inzwischen auch eine Feinzentrierung Plus für den Premium-Bereich. Diese verfügt über einen längeren Zentrierweg, womit auch höher bauende Kunststoffteile sauber entformt werden können. Die Premium-Variante bietet daneben auch noch weitere Vorteile. Unter anderem wird ein Messingkäfig eingesetzt. Messing hat den Vorteil, dass die Feinzentrierung Plus auch ein Ultraschallbad unbeschadet übersteht. Sie muss also nicht separiert werden.
Willkürlich auf der Formplatten-Oberfläche platzieren
Doch wie wird die Feinzentrierung Plus eingesetzt? Was sind deren Vorteile und wie sieht es mit der Wartung aus? Die Firma Braunform hat einige Anwendungen, über die in der Folge 4 gesprochen werden soll.
Der klassische Anwendungsfall zum Zentrieren der Spritzgiesswerkzeughälften. Die Feinzentrierungen der Normreihen 799x und 7980/1 können als höherwertige Alternative zu der Flachzentrierung verbaut werden. Die Funktionsweise ist markant anders, nämlich spielfrei und leicht abwälzend. Im Vergleich zur gleitenden Flachzentrierung hat man eine hohe Gestaltungsfreiheit, eine hohe Anfangstragkraft und sehr viele weitere Vorteile und Nutzen.
Guillaume Hopfner: Die Feinzentrierung Plus setzen wir ihn herkömmlichen Werkzeugen seit über 10 Jahren ein – und zwar bei allen Arten von Werkzeugen. Ob Ein- oder Zweikomponente, mit komplexer Entformung oder mit Schieber: Das System ist in der Werkzeug-Trennebene überall einsetzbar.
Klassisch werden vier grosse Flachzentrierungen in die Formplatten eingebaut und die Einsätze direkt über den Aufbau zueinander zentriert. Wir ersetzen diese durch zwei dieser Agathon Feinzentrierungen. Je nach Werkzeuggewicht auch mehr, so wie es im Katalog definiert ist. Der grosse Vorteil ist: Man kann die Feinzentrierungen willkürlich auf der Formplatten-Oberfläche platzieren – sogar mit kurzem Abstand – und trotzdem erreichen wir eine hohe Präzision. Durch die robuste Bauweise ist die Standfestigkeit sehr hoch.
Stefan Nobs: Sie sprechen die hohe gestalterische Freiheit an, was bedeutet, dass man die Feinzentrierung dort platzieren kann, wo man Platz hat. Wenn ich die Konstruktion betrachte, über die wir sprechen, sehe ich, dass die beiden Feinzentrierungen links und rechts angeordnet ist. Wie kam es dazu? Was für Überlegungen haben Sie hier gemacht?
Guillaume Hopfner: Dafür gibt es zwei Gründe. Im Formenbau mögen wir es nicht, wenn Elemente im Fallschacht überstehen, und zwar wegen der Verschmutzungsgefahr der Kunststoffteile. Und zweitens sind wir bei manchen Kunden oder in manchen Ländern auch nicht sicher, wie die Kühlleistung erbracht wird. Dadurch entsteht die Gefahr, dass beide Formplatten sich unterschiedlich ausdehnen. Deshalb wollen wir den Abstand zwischen den Feinzentrierungselementen geringer halten, da das Werkzeug sehr lang ist. Und mit «sehr lange» meine ich eine Länge von über einem Meter.
Limitierter Wärmesprung zwischen den Werkzeughälften
Stefan Nobs: Sie sprechen das Thema an mit der unterschiedlichen Ausdehnung der beiden Werkzeughälften. Wir wissen, dass diese Befürchtung im Formenbau sehr tief verwurzelt ist und dass da die Flachzentrierung gewisse Vorteile bieten kann. Wir haben dies deshalb auch genau untersucht, ob es wirklich einen Wärmesprung gibt von einer Werkzeughälfte zur anderen. Das Resultat hat unsere eigenen Annahmen und Theorien bestätigt.
Es zeigte sich nämlich, dass die beiden Werkzeughälften, wenn es geschlossen ist während des Einspritzprozess, sich temperaturmässig komplett zueinander abgleichen. Somit ist dieser Wärmesprung sehr limitiert. Die unterschiedliche Wärmeausdehnung und die Feinzentrierung können auch nicht gross zueinander verspannen. Was man dazu noch sagen kann: Die Feinzentrierung ist nicht unendlich steif, also sie kann gewisse Unterschiede auch zueinander ausgleichen.
Für mich noch eine weitere Frage, die ich gerne aufbringen würde: Sie haben da auch von exakt zentrieren gesprochen. Was heisst für sie «exakt» im Formenbau?
Guillaume Hopfner: Exakt zentrieren heisst bei uns auf jeden Fall unter einem Hundertstel zu sein, damit die Trennungen geschützt werden. Es gibt immer auch Positionsfehler durch die Bearbeitung der Aufnahmetaschen und den Einsätzen. Aber hier haben wir einen weiteren Vorteil mit den Feinzentrierungen plus, und zwar, weil die Kavitätentasche im selben Bearbeitungsvorgang mit der Zentrieraufnahme gefertigt wird. Die Zentrierungselemente sind letztlich dann nur ein Glied in der ganzen Zentrierkette – die weiteren Elemente im Werkzeug sind genauso wichtig.
Wiederholgenauigkeit im Sub-Mikrometerbereich
Stefan Nobs: Ja, das stellten wir auch fest: Das Verständnis mit dieser Zentrierkette – wir nutzen hier auch den Begriff «Anschlusskonstruktion» – ist wichtig zu betrachten. Wir haben zudem untersucht, wie präzis so eine Feinzentrierung ist. Wir konnten feststellen, dass die Wiederholgenauigkeit im Sub-Mikrometerbereich ist. Es waren um die 0,3 Mikrometer, was sehr genau ist. Das heisst mit anderen Worten: Im Formenbau muss man diese ganze Kette, diese Anschlusskonstruktion, genau anschauen. So erhält man dann als Resultat die Exaktheit, die Sie erwähnten.
Für mich stellt sich dann auch noch eine weitere Frage: Es geht auch um Zentrierkonzepte. Wenn möglich, möchte man schwimmende Kavitäten aus Kostengründen vermeiden. Aber wo ist dann die Grenze? Wenn man eine Schliessgenauigkeit von einem hundertstel Millimeter hat, muss man dann eine schwimmende Kavität anstreben? Oder wo sehen sie die Trennung, bei der man «schwimmend» gehen muss?
Guillaume Hopfner: Ja, ab einer gewissen Grösse gehen wir ohnehin auf schwimmende Lagerung über. Das ist die der sicherste Weg, um das Werkzeug zu bauen und die Genauigkeit zwischen den Kavitäten hinzubekommen.
Feinzentrierungen benötigt sehr wenig Schmierung
Stefan Nobs: Ich möchte noch die Wartung und Tribologie erwähnen, denn auch hier gibt es sehr grosse Unterschiede: Gleitende Flächen muss man dauernd schmieren und trotzdem kommt der Schmierstoff gar nicht an die Schmierstelle. Das ist eigentlich bei der Flachzentrierung der Fall, denn die Werkzeuge fahren aufeinander zu, dann wird plötzlich zentriert. Man hat keine Überlappung der Flachzentrierung: Wenn die Flachzentrierhälften aufeinandertreffen, wirkt dies durch den Versatz fast wie eine Kollision. Es besteht am Zentrierstart nur ein Linienkontakt und dort ist die Flächenpressung gewissermassen unendlich hoch und damit wird bereits die Oberfläche der Flachzentrierung zerstört. Nachdem die Flachzentrierung vielleicht ein Drittel Überlappung hat, kann man davon ausgehen, dass doch ein wenig Schmierstoff die Schmierstelle erreicht und das ganze System anfangen würde zu funktionieren. Aber eben auf dem ersten Drittel wird viel Abrieb erzeugt und dieser Abrieb wird eingewalzt in die Flächen und auch vermengt mit dem Schmierstoff. Das alles ergibt einen ziemlichen Abrieb, der insbesondere im Reinraum nicht erwünscht ist.
Hier setzt die Agathon-Lösung ein, und zwar mit der abwälzenden Feinzentrierung. Diese benötigt sehr wenig Schmierstoff, eine sogenannte Mindestmengenschmierung ist ausreichend – je nach Viskosität des Schmierstoffs, den man einsetzt. Schlussendlich muss sich der Kunde zwar selbst ein Know-how aufbauen, wie oft die Feinzentrierung geschmiert werden muss. Ich denke aber, das ist nicht mehr als wöchentlich, vielleicht sogar nur zweimal im Monat.
Für mich ist das ein wichtiger Vorteil. Gerade heute beim Fachkräftemangel müssen solche Werkzeuge auch autonom laufen können. Wie sehen Sie das?
Guillaume Hopfner: Genauso. Die Monteure in den Wartungsabteilungen sind erst einmal verwundert, wenn wir ihnen erklären, wie wenig Schmierung eine Feinzentrierung Plus von Agathon benötigt. Sie sind es gewohnt, täglich zu fetten. Hier liefert Agathon übrigens klare Anweisungen auch bezüglich Wartung, Reinigung und Schmierung – und seit wir diese Anweisungen der Werkzeug-Dokumentation beiliegen, haben wir noch weniger Ausfälle bei Agathon Zentrierungen als ohnehin schon.
Stefan Nobs: Apropos weniger Ausfälle und hohe Lebensdauer – da muss ich noch etwas erwähnen. Am Anfang, wenn das Werkzeug zentriert werden soll, ist ja eine Hälfte hängend. Diesen Umstand haben wir konstruktiv entgegengewirkt, indem wir bei der Feinzentrierung Plus einen fast zweifachen Rolleneintritt bewerkstelligt haben. Also einen Mechanismus entwickelt für eine hohe Anfangstragkraft, sodass praktisch zwei Rollenreihen sofort in den Eingriff kommen.
Damit man sich das auch bildlich vorstellen kann: Unsere Rollen haben eine hohe Tragkraft wegen des Linienkontakts. Eine Rollenreihe ersetzt gewissermassen acht Kugelreihen. Wenn wir dann gleich zwei Rollenreihen miteinander zum Tragen bringen, dann haben wir entsprechend sechzehn Kugelreihen, die helfen, das Werkzeug gleich am Anfang anzuheben. Und ich denke, das ist auch das Geheimnis, warum wir so hohe Lebensdauer ermöglichen. Und ich denke, für Sie könnte das auch wichtig sein mit Ihren Kunden in der Medizintechnik und Pharmaindustrie.
Guillaume Hopfner: Ja, das ist sogar essenziell. Es hilft, Partikel zu vermeiden, insbesondere im Reinraum. Bei eingelaufenen Flachzentrierungen kann man zudem immer erkennen, dass diese von vorne her verschleissen. Da gebe ich Ihnen absolut recht. Zudem ist es schwierig für uns, einen genauen Zeitpunkt zu definieren, ab wann die Flachzentrierung als verschliessen gelten, denn sie haben ja von Anfang an Spiel.